Green Coffee Processing
Western Technology delivers efficient and controlled technology processes, equipment and plants for handling and storing green coffee
TURNKEY PROJECTS
Western Technology add Value from the Coffee Plant to the Roasted Bean
Our supplier designs and manufactures machines and equipment for green coffee processing to the highest engineering qualities and standards under European standards.
In-depth product knowledge and expertise in the most modern processing technology and plant design ensure optimum processing of your coffee at low energy consumption.
This guarantees that your plant and equipment will reflect the state of the art in performance efficiency and final product quality.
Western Technology delivers efficient and controlled technology processes, equipment and plants for handling and storing green coffee. The processing equipment and solutions are based on thorough technical experience and comprehensive product knowledge.
Our custom-designed solutions ensure a more efficient coffee production process which will further enhance and improve the quality of your final product while applying focus to energy efficiency and improved cost-effectiveness.
Western Technology can deliver efficient and controlled technology processes, equipment, and plants for handling and storing green coffee. Our custom-designed solutions ensure a more efficient coffee production process which will further enhance and improve the quality of your final product while applying focus to energy efficiency and improved cost-effectiveness.
We can offer our clients the following process installations for improved productivity, efficiency, and quality:
- Green grain reception intake,
- pre-cleaning (cleaners, destoners, etc),
- hulling and polishing,
- grading and sorting (Screen grading, gravity separation, optical sorting, color sorting…),
- conveying and storage (coffee handling, silo cells rectangular, angle and chain conveyors, belt, screw, loading chutes, pendulum bucket elevators, and square piping systems.
- aspiration (dust filter systems, dust aspiration piping systems, etc…),
- control and automation (SCADA system, traceability, service program,…),
- temperature monitoring system
- and drying coffee (in an industrial vertical dryer).
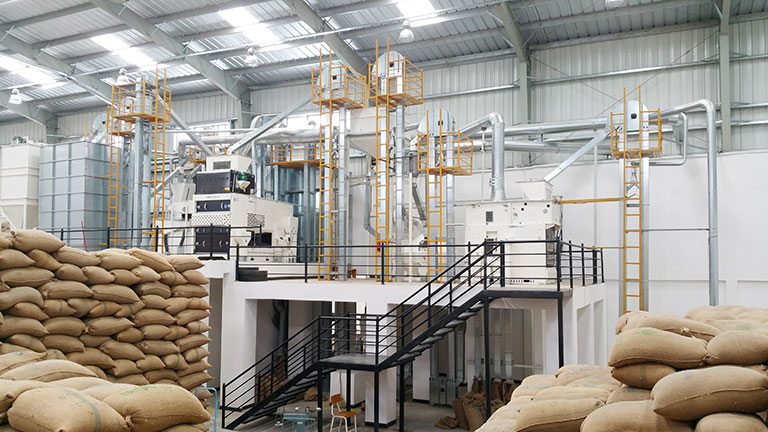
If it could be of interest to you, please contact us and provide us with all the necessary details for a pre-study.
Coffee hulling occurs during the initial stage of green coffee processing; it is usually done between pre-cleaning and size grading.
The hulling process removes the parchment skin from the coffee bean. The process is carried out very gentle at low temperature.
Polishing is an optional process where any silver skin that remains on the beans after hulling is removed by machine.
Polished beans are considered superior to unpolished ones. The polishing process is carried out in order to bring forth the beautiful deep color of the roasted coffee bean.
Hulling
The mechanism used by the huller machine is simple, with the coffee being fed through the hulling cylinder and filtered through the perforated screen using cross beaters. This helps to reduce the friction between beans and to restrict the generation of dust, thus resulting in minimum loss of product due to breakage.
Polishing
The green coffee beans enter the polisher through the inlet, where the throughput rate is controlled by means of a slide gate. The coffee beans are caught by the spiral windings of the rotor towards the outlet. During conveying, intensive husking and polishing takes place. The degree of polishing is controlled at the weight-load retarding gate.
Grading
Grading into many different fractions is sophisticated precision work. For the final sorting process, we have developed a unique technique for sorting according to length, thickness, width, weight, shape and colour. During the grading process, seeds of almost identical size can be separated into more than 900 different sizes in increments as small as 0.05 mm due to the huge varitey of screens that we have.
Flat screen grading
When using a flat screen grader, width and thickness grading will be carried out by combining the optimum screen aperture and screen slope with the length and frequency of the stroke. The product will be separated into the different fractions required. In terms of grading, in particular, Western Technology’s unique multiple flow diagrams in our graders outperform the rest of the market.
Gravity separation
The product processed by the Gravity Separator is separated into layers with different specific weights according to the “fluid bed” principle. The deck is fluidized by a completely uniform pressurized air system stratifying the light material to the top of the product bed and allowing the heavy material to come into contact with the deck surface. The deck is inclined from side to side and inlet end to discharge end at adjustable angles.
Optical Sorting
Using the very latest technology, Western Technology optical sorter will remove green coffee kernels having a different colour or exhibiting visual damage. Equipped with full-colour RGB cameras and LED lighting system, the optical system fulfils the needs of modern seed processing systems that demand the optical sorter’s ability to detect and reject seeds having either non-conforming colours or shapes.
Colour Sorting
In the optical sorter, the feeding system carries seed through oblique chutes where the flow is further divided and controlled. The kernels then fall through an analysis section where each kernel is checked by a number of optical devices facing each other. A colour-characteristic electrical signal is led to a control unit, which then converts the signal. Should non-designated particles be present, these are shunted off to the discard bin by means of an air blast fired by ejectors. The sorters are controlled by micro processors and their sophisticated software allows the use of up to 600 different sorting programmes to be stored on board.
EXAGON APP
A user-friendly and intuitive graphic interface enables easy and fast programming and control, and makes it possible for the operator to monitor the machine status through its synoptic.
Conveying equipment links the process line
In green coffee processing plants, conveying equipment links the various processes into complete production units. Conveying does not in itself add value to the seed. Nevertheless, correctly designed and gentle conveying solutions are crucial to the quality of the final product and therefore unquestionably safeguard value and create profit on the bottom line.
Storage
For storage, Western Technology offers a wide range of silos that are tailor-made according to the actual requirement of the project concerned. Western Technology silos, with their smooth walls, ensure genuine storage of valuable green coffee kernel without the risk of admixture. Aeration and cooling systems, supported by Western Technology’s temperature monitoring system, eliminate the risk of losses and damage to the coffee during storage. Intelligent filling systems with gentle let-down ladders preserve the kernels during filling.
Conveying and Storage
The Western Technology product line contains screw, belt, angle and chain conveyors, loading chutes, bucket elevators, pendulum bucket elevators and square piping systems.
Silo Construction
The silo cells are rectangular in a modular system. The cells are constructed to prevent kernel lodging. The sizes and number of the cells are determined in accordance with the requested number of different charges and batch size.
Dust Filter System
Dust appears in all green coffee plants, especially at the transfer points where the kernels are conveyed from one machine to another. Dust and bee wings are separated from the kernels and create an unpleasant and dangerous environment for the workers, including the risk of a dust explosion. Therefore a correctly dimensioned and integrated aspiration system is an absolute must in any modern green coffee plant. The dust filters are equipped with filter bags which separate the air before discharge to the atmosphere.
Dust aspiration piping must be properly designed according to air quantity, air velocity and pressure. The fans create the negative pressure that extracts the air from all extraction points. The air-locks discharge the dust to either a bag or to a conveying system to a dust bin. The red dust from the treatment process requires separate dust filters. These filters are equipped with collection baskets, as the toxic waste must be disposed of in a safe manner.
Control and Automation
A modern facility is not utilised in an optimum manner without an effective and reliable control system. A Western Technology control system combines our many years of process experience with the latest technology. This is your guarantee that all installed machines operate at their optimum performance, thereby ensuring the best economy of the entire system throughout the lifetime of the plant.
Scada System
The SCADA system is tailor-made for operation, monitoring and alerts and it can be controlled by the operator from one or several locations. In order to facilitate daily operation, all routes are saved and can be easily accessed. Our preferred system is WinCC from Siemens – a powerful, userfriendly, high performance PC based Human-Machine Interface (HMI) together with Microsoft Windows.
Traceability
The green coffee kernels represent great value, and thus traceability is extremely important. A stable and proven database system is normally set up in Microsoft SQL. Logging is typically done using a barcode system, but other systems such as RFID are also available.
Service Programme
To minimise the risk of breakdowns and plant downtime, operating statistics on each machine can be set and monitored, enabling scheduled service and preventive maintenance to be carried out on time.